Structural mechanics
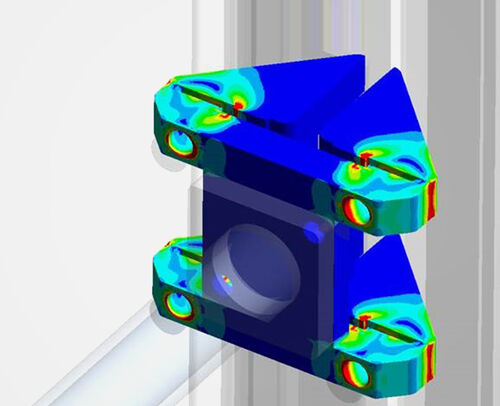
Defects or errors in a product series can often be avoided. Professional virtual engineering helps to detect weak points and to identify possible sources of faults or defects early in the process.
A FEM calculation allows for a targeted process and structure analysis in the early stages of development. The results of a structure simulation for example form the basis for further optimization processes to improve material usage and strength. Carefully planned and executed FEM calculations therefore facilitate the optimal use of resources in production and materials and increase the competitiveness of your product.
We offer static linear and nonlinear analyses, from individual components to complex assemblies including nonlinear contacts, material behaviour and large deformation.
Linear static analysis
Nonlinear analysis
Buckling
Strength verification statics and fatigue
Welds
Linear static and nonlinear simulation
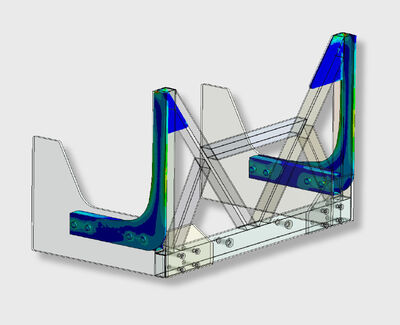
Linear static simulation
The linear static simulation shows stresses, strains and deformations, provided that the load is constant over time, that the component is only slightly twisted or deformed under load and that the material shows a linear stress-strain behavior.
Nonlinear Simulation
Taking into account lifting contacts, large deformations and nonlinear stress-strain behaviour of the materials considerably expands the scope of realistic modelling. Thanks to powerful software and affordable computer performance, even complex tasks with regards to static analyses with nonlinear contacts, materials and significant deformations can be processed in an economically viable way.
Verification of Stability / Buckling
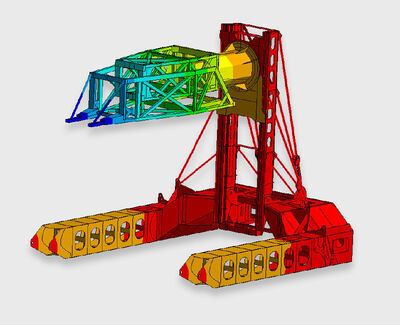
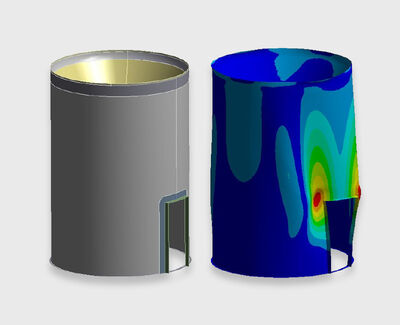
Strength verification – statics and fatigue
A strength verification is an important element in the process of developing components for technical systems. It is used to prove and document the eligibility and suitability of newly designed components to make sure they can fulfil their intended purpose. A current set of rules for strength verification in mechanical engineering is the FKM guideline that is applicable to components made of steel, cast iron and aluminium materials. The main difference and benefit of the FKM guideline compared to more traditional regulations is the concept of applicability with regards to local stresses, which are usually available as results of an FEM simulation. This procedure is described for the static strength verification as well as the fatigue test. The safe use of a product over a defined life cycle is a crucial prerequisite for the product to enter the market.
Proof of stability: bending and buckling
The failure instability is defined as bending (rod-shaped parts) and buckling (surfaces). If bars, panels, boards or shells are subjected to pressure, above a certain intensity the state of equilibrium is no longer stable which means that the structure buckles, bends or bulges. In a simulation, this requirement is represented by a linear eigenvalue buckling analysis and nonlinear analyses with regards to plasticity and significant deformation.
BENEFIT FROM OUR EXPERIENCE.
WE LOOK FORWARD TO HEARING FROM YOU.